Founded in 1943, in the midst of World
War II, Revell's staff of talented artists, sculptors, machinists, chemists,
engineers, researchers, instruction writers, and assembly line workers have tuned
out multiple millions of highly detailed scale plastic models of every mode of transportation
ever devised, from every country that devised said modes of transportation. Revell
also made scale scenery and people to compliment the models. They even made model
of things that never really existed, like star ships and submarines that could explore
20,000 leagues under the sea. I use images from the box tops of many Revell kits
for the Airplanes and Rockets website daily logos (it's free advertising for them).
Monogram (founded
in 1945) and Revell merged in
1986. Hobbico, familiar to many
R/C airplane modelers as the parent company of
Tower Hobbies, eventually bought Great
Planes, Estes, Dynaflite, Thunder Tiger, and a few other recognizable names. Unfortunately,
Hobbico filed for bankruptcy in 2018, and now barely exists after being taken over
by the Horizon Hobby folks.
Revell Shows Production System - How Plastic Kits Are Made
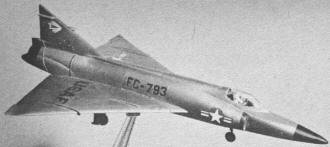
Assembled Convair F-102 Delta Dagger model
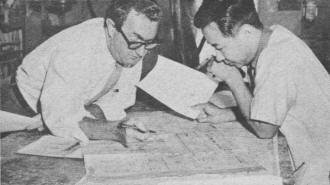
Authenticity starts with research. Jack Campbell (left), research
head, shows model maker material gathered for making of HMS Bounty kit. Search for
original blueprints and data often sound like a detective story. This is especially
true in the case of old time sailing ships. Drawings for ships long out of operation
are sought by correspondence, talks with authorities in this field and from museums.
Word that a certain photograph or drawing was published in a book a half century
or more out of print, launches prowl through second hand book collections and libraries.
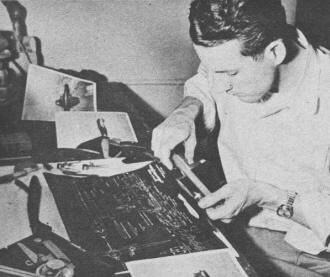
First step is building hand made model to serve as master for
dies needed to turn out plastic parts in volume. Model maker checks measurements
of master model against blueprints and photographs of Martin B-57B prototype.
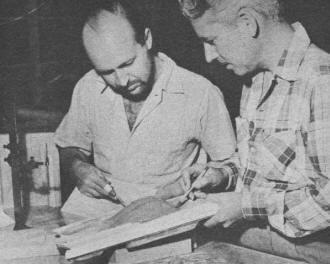
Construction of hand made model sometimes larger than finished
miniature kit helps capture detail. Models, made of wood, plastic, clay, or epoxy
rosin, take 5-6 weeks to complete. Bob Hoeppner (right), chief model maker, and
assistant check Lincoln Futura.
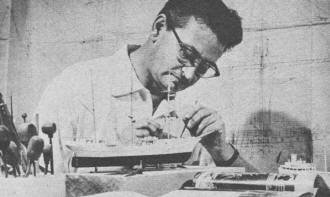
Tom Hogg, ship model specialist, puts finishing touches to Coast
Guard Training Ship Eagle. In this case 13 3/4" model is identical in size to that
which hobbyist will assemble. Official plans (in background) were obtained from
U.S. Coast Guard.
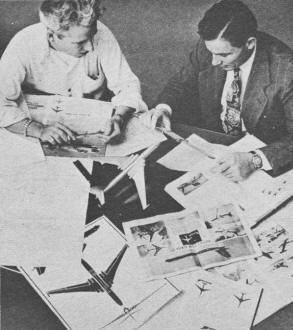
Director of Engineering Charles Gretz (right) and Hoeppner check
hand made model of Russian Bison Bomber. Information on this model was not easy
to obtain. Search went into many countries.
|

Included in many kits are miniature figures scaled less than
one inch to foot. Sculptor Harry Plummer completes 9-inch pilot to serve as master
from which molds for 31/32" plastic figure will be made.
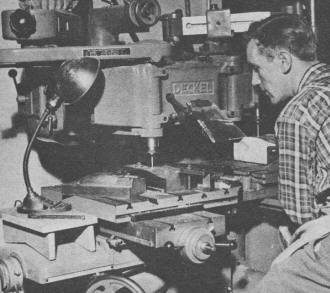
Plaster patterns from hand-made models serve as guides for duplicating
larger parts of ship or plane in steel. Core of a ship's hull is cut into steel
from plaster pattern on 1-1 Deckel pantograph. Over forty man hours needed to produce
this one component.
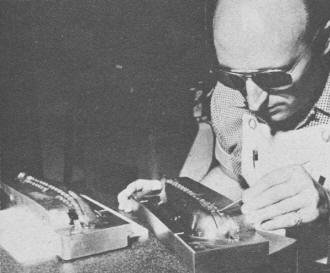
Mold maker adds final touches to U.S. Constitution steel production
mold. Over 9,000 man-hours required to tool steel dies for this kit of 174 parts.
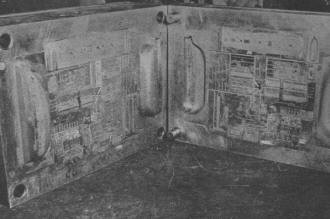
Steel mold for HMS Bounty ready to be closed up, preparatory
to being placed in injection molding machine. Center sprue through which heated
plastic is injected is in center of mold. Small runners radialing out from center
carry plastic to cavities, filling each part. Only enough plastic for one "shot"
is injected into machine during each molding cycle which produces a kit in 30 seconds.
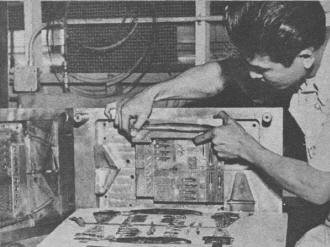
After mold's first soft test-run in injection molding machine,
each part of plastic "shot" is re-checked. Tolerances of .002" are normally maintained.
When final mold corrections are made, steel is hardened by special heat-treat method.
Toolmaker reassembles components of production mold for Martin B-57B; taped on board
are first test "shots."
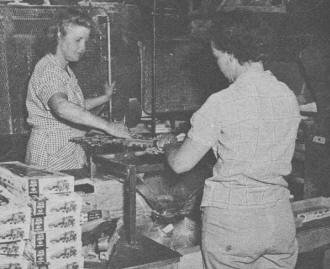
Every 32 seconds Mobilgas truck parts come out of this hydraulically
operated injection molding machine. Packing is done at the machine by operator who
separates parts from plastic runners. Parts drop from hopper into polyethylene bag
which is heat-sealed; bag goes into box with instruction sheet and decals.
|
Posted February 1, 2020
|