The type of glass referred
to in this 1953 Science and Mechanics magazine article is not the solid
sheet type made from sand (silicon), but fiberglass. It has strands of glass
mixed into the plastic weave, hence the name. It is the glass component that
causes itching as it pricks your skin. Breathing it into your lungs is dangerous
as the minute particles of glass can lodge in the tissue. Typical of the era,
the workers shown handling the fiberglass have no protection for eyes, nose,
mouth, or skin. Fiberglass ended up not being the material hoped for because it
ultimately could not stand up to the extreme structural and thermal loads
typical of high speed aircraft. It was also not tolerant of being exposed to
intense sunlight while sitting on a tarmac. The few commercial and homebuilt
fiberglass airplanes need to be painted white to reflect as much ultraviolet
light as possible to prevent delamination and deterioration of the components.
Carbon fiber on the other hand, which came about decades later, has proven to be
useful.
Glass-Plastic Aircraft Challenge the "Heat Wall"
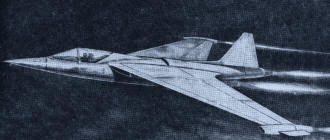
Artist's conception points up the tigerish grace of the ultrasonic
glass aircraft of the future.
By James Joseph
"The plane of tomorrow will be glass, probably glass fabrics impregnated with
resins. We're not even thinking or designing in terms of metal anymore."
This remarkable prediction by Thomas E. Piper, Northrop Aircraft's director of
materials, is echoed by other materials experts in the field of aircraft design.
And the facts - including data on superior heat resistance and lower costs - are
there to back up the statement, which refers to military planes and, indirectly,
to civilian aircraft.
This "substitute for today's aluminum airplane skins," as Piper puts it, consists
of half a dozen layers of glass fabric, impregnated with phenolic resins and cured
in a heated mold. Such a fiber-glass-plastic laminate is the sleek clothing that
the well-dressed jet or rocket plane of 1958 may wear. It's a good bet that smaller
private planes also may be decked out in glass and plastics bi that time, and they
may sport a lower price tag, too.
The immediate reason for pushing the development of fiberglass-plastic laminates
is the fact that aluminum aircraft skins will not stand up under the high temperatures
generated by air friction at the super-sonic and ultra-sonic speeds our planes are
beginning to attain.
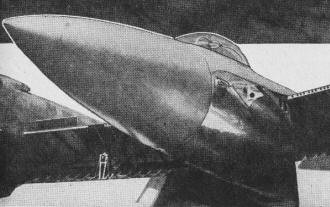
End result of glass-plastic molding is this sleek, clean tailcone
of laminated glass fabric. No riveting - a costly, time-consuming job - was required.
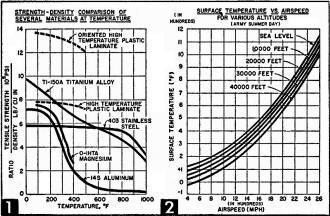
This chart (Fig. 1), released here publicly for the first time,
shows why metals can't be used for skins on jet planes that will ram the friction
barrier at twice the speed of sound. Aluminum and magnesium lose their tensile strength
as temperature rises. Titanium alloy is too expensive and stainless steel is too
heavy. Glass-plastic laminates probably hold the answer.
Fig. 2 illustrates how surface temperatures of plane's skin increase
with the air speed at various altitudes.
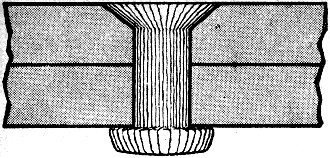
Glass rivets - as designed for the future - will be necessary
to maintain uniform expansion of fastener and material during high-speed flight.
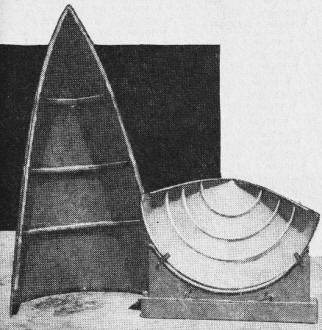
Glass laminate tailcone, fabricated in two pieces in mold, emerges
after the baking process looking like this.
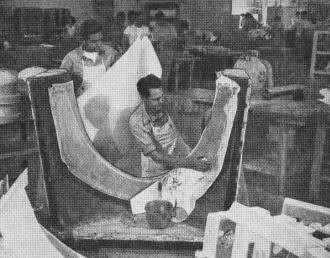
A workman in Northrop's plastic shop impregnates cloth in mold
before laying on the pre-cut glass fiber.
Can glass take these temperatures? Certainly not ordinary glass, which is brittle,
cracks under sudden heat shock, and is unable to endure wide temperature variations.
But bond several sheets of fiberglass with a phenolic resin and you come up with
something else again. The most valuable characteristics of this material, in comparison
with aluminum, for instance, is its ability to retain a much higher percentage of
its tensile strength after prolonged exposure to temperatures in the 500° F.
range (Fig. 1).
That, briefly, is the "why" behind the development of glass-plastic skins for
military aircraft. A parallel result probably will be the production in a few years
of better, cheaper small planes for private use. As a matter of fact, that picture
already is beginning to come into focus.
Hundreds of aircraft parts are being molded from glass fabric right now, including
various airs coops, tubing, and entire sections of some classified military planes.
Some British manufacturers estimate that use of the laminates for small plane skins
would reduce their overall cost by 30%. Northrop engineers expect "at least 25%
reduction."
All other things being equal, that could mean that in 10 years the glass-skinned
counterpart of a metal plane that now sells for about $19,000 will be available
for a little over $13,000. The plane that retails today for $13,000 may be priced
as low as $9,000 when it's produced in glass-plastic, assuming of course, that other
costs remained constant. This envisions, also, a more simply constructed fuselage
that perhaps would be molded as a single unit. Of course, these glassy jobs can't
- and probably won't - compete price-wise with the fabric-and-dope-skinned models,
that sell now for prices ranging from about $3,700 to $7,000.
Designers visualize the supersonic plane of 5 to 10 years hence as having fiberglass-plastic
wings, ailerons, stabilizers, fuselage, and even fiberglass rivets fastening its
laminated glass skin to its titanium and stainless steel low-density frame. Fuel
will have lower vapor pressure than any today so as not to boil at speeds in excess
of 2,000 mph. Dry, heat-resistant metal powder will lubricate the plane's powerful
jet engines.
This is no dream. The British hope to flight-test a glass-covered plane this
year, and numerous U. S. experimental planes already have been built with portions
of their fuselages and .wings fabricated from plastic-glass fabric.
All this is a clear admission that having overcome the sonic barrier (smashed
in 1947 when U. S. Air Force Capt. Charles E. Yeager shuttled his rocket-engined
Bell X-1 some 1,100 mph), airplanes have run smack into another - the thermal barrier
(also dubbed the "Ram Compression Temperature Rise" and "heat wall"). Overcoming
the thermal barrier means revolutionizing the basic ingredients of modern aircraft,
to withstand the terrific temperatures generated by friction when a plane hurtles
through space at double, triple and quadruple the speed of sound. As the speed of
a plane is doubled, its friction-temperature quadruples. Thus, at 1,000 mph (and
at 40,000 ft.), a plane's skin is a feverish 120°F. At 2,000 mph, skin temperature
is a red-hot 575° at 40,000 ft. and a sizzling 700°F. at sea level (Fig.
2).
Magnesium and aluminum alloys lose their stiffness and become pliable at 500°F.
Both melt between 1,200-1,400°F. Titanium is too expensive ($20 a pound) and
scarce. Stainless steel is too heavy for aircraft covering. It appears that metals
are fine as long as you're poking through the atmosphere at not over 1,500 mph,
but none of today's metal-skinned, piloted aircraft designed for sustained flight
could stay in one piece much over 1,800 mph. The ship's aluminum skin would soften
from the terrific heat. In a matter of minutes the plane would rip apart in mid-air.
You've read about unsolved instances where faster-than sound aircraft exploded
during power dives - and some of the "flying saucer" interpretations of why these
planes disintegrated. A more realistic picture would be, that during a high-speed
dive the ship crossed the threshold of "safe" supersonic speeds. Its aluminum skin
softened under the terrific friction temperature and burst like a ripe melon.
Our fastest fighters are approaching thermal barrier speeds now (1,600 mph and
a friction temperature of 500°F. at sea level). Our old standby, aluminum alloy,
has a nervous break-down at supersonic speeds in the Mach II range (1,500 mph and
above). At room temperatures its tensile strength is 62,000 lbs. per square inch.
Preliminary tests show that after only a few minutes at 500°F., its strength
falls to 18,000 psi - a loss of 70%. Today's aluminum skins, subjected to the 500°
test for a full 24 hours, lose nearly 90% of their strength. Magnesium alloys aren't
much better.
On the other hand, glass-fabric laminates with a tensile strength of 80,000 psi
at room temperature, have been found to lose few or none of their mechanical properties
at 300°F., and only 20% strength after exposure for 24 hours at 500°F.
The materials weight-strength chart (Fig. 1) reveals why metals are doomed as
aircraft covering, and why glass fabric will come into its own. Aluminum would have
to be 7% times as heavy (and many times thicker) than a given thickness of ,glass-plastic
to withstand sustained temperatures of 500°F. Oriented glass-plastic fabric
(with its glass fibers rigidly controlled and aligned) can be 11.5 to 12 times lighter
than aluminum - yet retain much of its strength at 500°F. The weight of a material
compared to its strength is a big and decisive factor in choosing any new material
for airplanes.
Glass fabric's insulating and non-corrosive features are other big advantages.
Today's all-metal aircraft are heat conductors. Even a few degrees temperature rise
on the airplane's skin is transmitted throughout the craft - and turns an unairconditioned
cockpit into a hot box. Glass and plastic are poor heat conductors.
"Fact is," says Piper, "after glass, we'll probably experiment with asbestos-covered
planes. The British already have worked with asbestos." But asbestos won't be needed,
some designers believe, until planes fly so fast that their skin temperatures soar
to 1,000°F. (2,600 mph at sea level).
Simplified Production
Glass fabric-phenolic laminates should revolutionize production methods, too.
Today's aircraft contain thousands of rivets which hold their aluminum skins together.
Skins are pressed from sheet aluminum very much as are automobile bodies. After
or before forming, the metal is machined and rivet holes are drilled. All this means
hours and hours of machining - most of it precision stuff requiring skilled hands
of which there's always a scarcity.
Using glass-fabric, most of the machining and drilling would be eliminated. First
comes a mold - a huge plastic cast. Into this are fitted layers of pliable fabric,
each layer "glued together" with the adhesive-like phenolic resin. When the layers
are built up to desired thickness, the mold is compressed and heated under 15 to
800 pounds of pressure per square inch to give the necessary tensile strength.
One of the difficulties to be overcome is the fact that glass fabric, despite
its other sterling qualities, doesn't stand up too well under wind erosion - the
factor that creates the friction-temperature in the first place. The aircraft designer,
like the farmer, is deeply concerned with the problem of erosion.
"Maybe," says Piper, "we'll have to mold very thin stainless steel foil to the
exterior glass skin, especially on leading wing edges." Erosion becomes a serious
problem at Mach II (1,500 mph) and above.
Aircraft engineers already have launched research on fiberglass rivets and say
that although tests to date haven't been too successful, there's no reason why they
shouldn't work. Metal rivets aren't satisfactory for joining glass to glass, or
glass to a metal frame. The reason: At high temperatures metal rivets expand, and
at lower temperatures they contract. This loosens the rivets and diminishes structural
rigidity.
Fuels and lubricants also must change radically to meet new conditions of higher
speeds and heats. At two or three times the speed of sound, hydrocarbon engine fuel
(high test aviation gasoline) boils. Various methods of refrigerating fuel tanks
have been suggested, but all involve added weight. The need is to develop a readily
available fuel having such a low vapor pressure that it will not boil at high temperatures.
High-temperature lubricants probably will be of the metallic dry-powder or dry-film
types-such as molybdenum disulfide.
In the next few years big things will be coming out of our aircraft plants. And
I don't mean just the B-47. Dead ahead looms the thermal barrier, and with it the
era when glass-plastic-and perhaps asbestos - will replace conventional metals.
Posted June 8, 2024
|