Young
Men • Hobbies • Aviation • Careers magazine, which had a run of 13 editions, ran a feature called "You Ask... The Experts
Answer," whereby questions from readers on a variety of subjects were answered by experts in their corresponding field.
Mr. G. Harry Stine, who would a couple years later would write the monthly column "Rocket Trails" in American Modeler magazine, fields
a reader's question on the difference between monopropellant and bipropellant liquid fueled rocket engines. Young Men,
by the way, was the title of publisher Street & Smith Publications' magazine between
Air Trails - Hobbies for Young Men and
American Modeler.
Thanks to Bob Balsie for scanning the pages.
What Can You Tell Me About Liquid Propellant Rockets?
You Ask ... The Experts Answer
The Question: Asks Charles Bennet of Somerville, Massachusetts. "My science club has been studying rockets. I'm a little
confused about the difference between bipropellant and monopropellant liquid rocket engines. Can you help me out?"
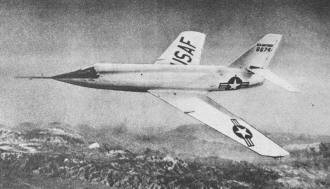
Curtiss Wright "throttleable" 15,000 lbs. thrust liquid propellant engine in supersonic Bell X-2 develops
almost as much power as a modern Navy cruiser.

Famous rocket pioneer, Dr. Robert H. Goddard, with world's first liquid fuel rocket which he built at
Clark University andd shot at Worcester, Mass., in 1928. He was first to pump propellants into firing chamber.
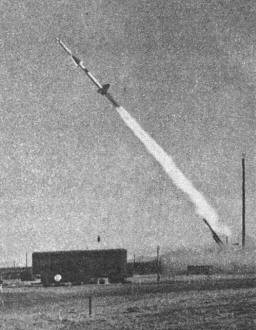
Launching of Army Nike missile is awesome undertaking to any spectator. Expert Harry Stine who answers
this month's query reveals "flame" from rocket tail is in reality a stream of high-speed gas molecules.
The Expert Answer: To get the basic facts on liquid propellant rockets we turn to a noted authority from the White Sands
Proving Ground, Mr. G. Harry Stine:
The solid propellant unit is the oldest form of rocket. But there is another type of rocket engine which was conceived
about 1920 to overcome the faults of the solid propellant rockets.
This second type is the liquid propellant rocket engine, called merely a "liquid unit" in rocketeer parlance. It is more
complex than the solid unit. Instead of carrying its fuel in solid form, it uses liquids and as a result is much superior
in many ways because liquid fuels contain more energy per pound of weight. Also, a liquid unit may be started and stopped
at will and can be used over and over again.
The two general types of liquid rocket engines are classified according to the type of propellant they use. A bipropellant
unit utilizes two liquids, one an oxidizer and the other a fuel. A monopropellant rocket engine has both oxidizer and fuel
combined in one liquid. The propellants of both types are injected into the combustion chamber where they atomize and ignite,
forming gas and heat. This is the same thing, essentially, that happens in an automobile engine, but a rocket uses the "products
of combustion" differently. Since the heat causes the gas molecules to move very rapidly in all directions, the object of
the rocket engine is to direct them in a rearward direction; this it does by means of the throat and nozzle of the chamber,
which converts these random molecular motions into movement in one direction. Every picture you see of a rocket shows flame
coming from the tail. In reality, for the most part this is not a flame but a stream of very high-speed gas molecules, all
glowing brightly.
Liquid fuels may be such things as ethyl or methyl alcohol, aniline, acetylene, gasoline, liquid hydrogen, or kerosene.
Oxidizers, on the other hand, are just what their name implies: they're rich in oxygen and constitute an "atmosphere" for
the fuel to burn in. This one of the main reasons a rocket can used in a vacuum; it carries its own atmosphere along with
it. Examples oxidizers are nitric acid, liquid oxygen (of course!), sulphuric acid, and hydrogen peroxide.
Monopropellants are sometimes very unstable things. Rocket men are wary of them because, containing both fuel and oxidizer
together, they have the habit of exploding with the slightest provocation. Nitromethane is one of the prime examples of
a monopropellant and has a killer's history. A fairly stable monopropellant is liquid ethylene oxide; in fact, it's so stable
that rocket men had trouble convincing anybody it would burn at all!
When propellants burn in the combustion chamber, they form large volumes of gas and a pressure is built up in the chamber.
In most rocket units, this "chamber pressure" is around 300 pounds per square inch, but in "high performance" engines it
may even be more. Under these conditions, you can't get propellants to flow into the chamber of their own accord; they must
be forced in. There are two commonly used ways of doing this, and they constitute a further sub-classification of liquid
units:
( 1) The propellants may be forced into the chamber by pressurizing the propellant tanks. This means the tanks must be
heavily built to withstand the pressure. Although this is the simplest method, the weight begins to become too great with
high performance units or big tanks, and a second method had to be worked out by rocket pioneers.
(2) Dr. Robert H. Goddard developed the second method around 1935 when pressure-feed systems reached the point of diminishing
returns. Goddard pumped the propellants into the chamber using a small centrifigal pump (like those on fire trucks and in
city water systems) which was driven by a turbine. There are many ways to drive this turbo-pump, chief among them being
the hydrogen-peroxide steam generator used in the V-2 rocket. The pump-feed system means you can use lightweight tanks with
a considerable saving of weight. This is the system employed in most of the big beasts like the Viking rocket.
* * *
What's your question? If it is of a technical, scientific or mechanical nature send it in to "You Ask," c/o Young Men,
304 East 45th Street, New York 17, N. Y.
Posted May 14, 2016
|