DISCLAIMER: This scanned version of
the Schweizer 2-33A Sailplane manual is provided
without warranty of completeness
or accuracy. It is solely as a service to builders of scale model
aircraft who are in search of reference material. Under no circumstances
should this reproduction be used as a guide for the operation of
a full-scale, human-occupied aircraft. Contact Sikorsky Aircraft
Corporation for copies of an official manual.
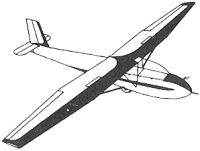
GENERAL DESCRIPTION
The SGS 2-33 is a conventional two-place tandem, intermediate-training
sailplane, manufactured by Schewizer Aircraft Corp., Elmira, New
York. Its construction is all metal with fabric cover on the fuselage
and tail surfaces. It has a one piece canopy for increased visibility.
The wings are tapered in the outboard section, and have dive-brakes
incorporated. Overall dimensions are: Length - 25'
9"
Span - 51' 0"
Height - 9' 3-1/2"
Wing View - 219.48 sq.ft.
Aspect Ratio - 11.85-1 (page 1-2)
Supplement No. 1 to SGS 2-33 Flight-Erection-Maintenance
Manual
FLIGHT CONTROLS- 2. Dive Brake & Wheel Brake (Ref.
Item 2 on Page 1-2) Beginning (page 1-2a)
5. Trim Lever (Reference Item 5 on Page 1-2) On sailplane
serial no. 500 and up, a ratchet-lock trim installation (P/N 33140G)
is provided, superseding the bungee-type trim found on lower serial-number
ships. The trim control lever for the ratchet-lock trim
system is located just forward and to the left of the front cockpit
control stick. The system is integral with the forward control stick
and torque tube assemblies. The
trim is operated with the fingers of control stick hand by aft pressure
on the locking lever. The control stick is then moved to the position
which gives the desired airspeed, at which point the locking lever
is released to engage the trim lock. Prior to take-off,
the trim should be set (locked) at the elevator-neutral position
which is checked by stick line-up with the trim placard neutral-arrow,
located on the floorboard to the left of the control stick.
After take-off, the desired trim settings may then be obtained
as noted above. Maintenance of the ratchet lock trim system
is limited to maintaining security of attachments and periodic lubrication,
with special attention to the spring-cartridge, per codes "A" and
"B", Page 2-5 of the Erection and Maintenance Instructions section
of this manual. There are no field adjustments to be made to the
trim system or the spring cartridge. (page 1-2b)
PREFLIGHT INSPECTION
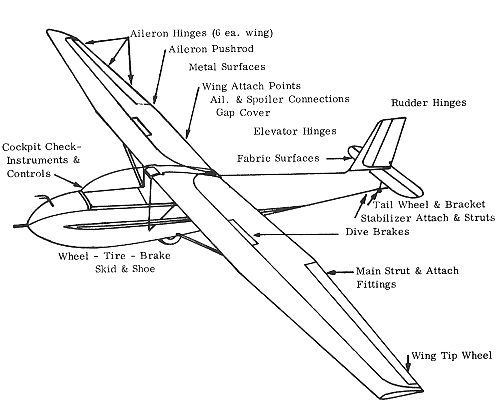
CHECK ALL POINTS AS LISTED1.
Wing: a. Strut
fittings b. Dive brake hinges and connections
c. Aileron hinges and push rod attachments 2.
Tail Assembly:
a. Hinge points, rudder and elevator b. Push
rod attachment to elevator horn c. Stabilizer
struts and stabilizer attachment to fuselage.
d. Rudder cable connection to rudder horn
e. Tail wheel assembly 3. Fuselage:
a. Release control b. Flight controls for
free movement including release c. Instruments
d. Canopy attach points and latch e. Safety
belts and shoulder harnesses f. Rear door
and window attach points and latches g. Fabric
for damage h. Wheel, tire and brake
i. Static and pitot tubes for water or other foreign objects.
4. Tow Rope:
a. Condition and attachment of rings. (page 1-4)
Precautions: 1. Be sure
equipment is suitable for purpose 2. Person driving car
or operating winch should be experienced with equipment and know
towing characteristics of the SGS 2-33. 3.
Never hook rope or wire to empty sailplane. Winch or auto
tows may be executed in the usual manner using either the forward,
or the CG release, although the latter should result in a higher
altitude. There is no tendency to oscillate with either release.
Maximum speed for auto, or winch tow. is 69 MPH.
CAUTION: 1. Do not climb at
full back stick position until a safe height for stall recovery
is reached (75 - 100 ft. ). 2. Level out before releasing.
Aero Towing: 1. Trim
(bungee lever) forward position recommended for solo take-off. 2.
You will notice that aileron control is somewhat heavy at fast towing
speeds, but they reduce to a normal level at
slower speeds.
FREE FLIGHT
Flying Speeds:
Best gliding speed (L/D) 23-1 at 50 mph . . . 2 place
" "
" (L/D) 23-1 at 45 mph . . . 1 place
Min. sinking speed 42 mph 3.1 FPS . . . . . . . 2 place
" "
" 38 mph 2.6 FPS . . . . . . . 1 place
Flight Limits-speeds: Dive
- 98 mph
Aero Tow - 98 mph
Dive brakes extended - 98 mph
Auto or winch tow - 69 mph Aerobatics:
Mild aerobatics to 80 mph can be done. Inverted flight prohibited.
Stalls:
Are very gentle and always straight ahead with no tendency to go
off to either direction. Buffeting
occurs before the stall 31 mph solo, 34 mph dual. (page
1-5)
Spins
The 2-33 will spin, depending on the weight of pilots and equipment,
etc., Care should be taken to
avoid stalls and spins at low altitude by using adequate air-speed.
Useful Loads
The placard weight/s on the instrument panel must be strictly adhered
to. This will insure that center
of gravity will be maintained in flight. The weights stamped are
maximums and minimums which are
easily compared with that of the pilot and passenger.
NOTE:
Seat ballast must be added if minimum weight of pilot! s is less
than placard minimum. Spiralling
In order to remain aloft or gain altitude it is necessary to spiral.
The diameter of a thermal is normally in
thermals
quite small, therefore, a fairly steep bank is required. Although
this is general practice, it may not be
necessary in areas where large diameter thermals are found. The
best flying speed in any thermal, at
any degree of bank, is a few miles per' hour above the buffet-before-the-stall.
Example:
SGS 2-33
Solo
Dual Stalling speed-level flight
31 mph
33 mph "
" -30° bank
33.5 mph 35.5 mph Buffeting
34-37 mph 35-38 mph Spiralling
speed
38 mph
42 mph
Keep in mind that the steeper the spiral, the higher the minimum-sink
and stalling speed will be. Sometimes it is
necessary to spiral very steeply and sacrifice slow speed and low
sink to remain within the limits of the thermal.
This is especially true in strong, small-diameter thermals.
Slipping The SGS 2-33 can
be slipped both forward, and while turning. The slipping-turn is
done in a normal procedure, but due to limited rudder area, the
forward slip must be done with very little low wing and full rudder.
The airspeed should be kept between 45 - 50 mph for fastest rate
of descent. (page 1-6)
Pattern It is general practice
to fly a traffic pattern. Downwind and base legs and final approach.
Extra speed is also used depending on wind velocity and gust conditions.
It is good practice to add 1 mph to airspeed for each mph of wind.
Spoilers Approach should
be made high, with use of dive brakes. Dive brakes increase sink,
which in turn makes a steeper and more controllable glide path.
They can also be used to lose altitude rapidly at any time during
a flight, or during a tow to take up slack, or to lower sailplane
from a too-high position. When flying solo, the stalling speed of
the 2-33 is 31 mph with dive-brakes closed and 34 mph with dive-brakes
open. For dual flight, the speeds are 33 mph and 35 mph, respectively.
It is unsafe, however, to make an approach with dive brakes
open in the speed range of 36 to 43 mph as the rate of descent is
so great that a proper flare-out for landing cannot be made.
Touch Down Can be done with
dive brakes either open or closed although it is preferable to land
with them open. With dive brakes open, the glide path is quite steep,
therefore, a flare-out must be executed 2 - 5 ft. above the ground
at 43 - 46 mph. By holding a level attitude close to the ground,
the sailplane will settle to a smooth, level touch-down.
DO NOT FLARE OUT TOO HIGH - this will
cause a very hard landing and may result in injury to occupants
or sailplane. Touch down with dive
brakes closed Is executed by letting the sailplane
land itself at, or near, 40 mph. Be careful not to ease stick back
after touch-down. This will cause a steeper angle of attack and
the sailplane will lift off. Taxiing
after touch down Even though sailplane is on the ground,
it should literally be flown to a stop with use of all controls.
Wheel brake may be used if a quick stop is desired or necessary.
(page 1-7)
Getting out of
the 2-33 On the ground it is tail down when empty,
and nose down with pilot in the seat. When pilot gets out he should
keep his weight on the side of the cockpit until he is in a position
to lower the tail gently to the ground.
GENERAL FLIGHT PROCEDURE IN STRONG WINDS
1. Be careful during ground handling operations.
Keep tail high to and from tie down area. 2. Keep well up-wind
of your landing area. 3. When going against wind, it is good
practice to add wind velocity to air speed at best L/D.
EXAMPLE
Speed at best L/D (solo)
45 mph
Wind velocity
+ 15 mph
Desired speed
60 mph This speed will give a better glide angle
than a slower approach. 4. Land into the wind whenever possible.
In crosswind landing, crab into the wind to maintain desired path
over the ground and at the last moment, straighten
ship to line of flight and touch down. Be careful while the ship
is rolling. Downwind landing in high winds
- Land with brake full on and maintain control as long as possible.
TIE DOWNS
The 2-33 should never be left unattended in strong winds or
gusty conditions. Tie down points are at each wing where main struts
are attached and at tail wheel bracket. Be sure ropes and stakes
used for tying down are adequate and in good condition.
(page 1-8)
Flight Limitations for 2-33 and 2-33A
In any aircraft, it is important to know the opera ling limits
and that exceeding these limits can highly endanger the aircraft
and its occupants. The following information is provided for the
2-33 and 2-33A at 1,040 lbs. gross weight. The speeds with
which you should be familiar are: Placard Speed (never exceed)
with or without Dive Brakes open 98 mph Placard
Speed (never exceed) for aero tow)
98 mph Speed to begin maneuvering with caution
65 mph Placard Speed (Never exceed) for auto or winch tow
69 mph In the 2-33, at speeds over 65 mph, the pilot must
maneuver with caution. The maximum load factor which should be attained
in flight is 4.67 G, and the pilot can easily exceed this in abrupt
maneuvers at speeds over 65 mph. The speeds between 65 mph and the
98 mph placard should be treated as a cautionary range and maneuvering
within this range should be gradually reduced to a minimum as velocity
increases. The 2-33 limit load factor of 4.67 should not
be exceeded in operation. A safety factor of 1.5 is required by
the FAA which gives an ultimate load factor of 7.0, but this safety
factor is required to allow for material variations and inadvertent
atmospheric conditions. Because of its light wing loading, a sailplane
can develop very high loads if speed limitations are not rigidly
adhered to. Normal category light airplanes are usually certified
to a limit load factor of 3.8 G's.
Understanding the Flight Envelope
The FAA required design flight envelope is presented on the
following page. On the horizontal axis are indicated velocities
in miles per hour, and on the vertical axis are load factors expressed
in "G" units. 3. When going against wind, it is good
practice to add wind velocity to air speed at best L/D. 4. Land
into the wind whenever possible. In crosswind landing, crab into
the wind to maintain desired path over the ground and at the last
moment, straighten ship to line of flight and touch down. Be careful
while the ship is rolling. The straight lines labeled "gust load
factors" represent the effect of the FAA required 24 ft. per second
gust on the sailplane as speed varies. They diverge from the one
"G" situation where the glider would be at rest or in perfectly
balanced level flight. The curved lines diverging from zero "G"
represent forces which can be induced by moving the elevator (or
other) control abruptly at various speeds. As you can see, the faster
you fly the more effect moving your controls will have. Gusts will
also have more effect as speed increases. The speed for maneuvering
with caution occurs where "G" loading from an abruptly moved control
meets the 4.67 limit load factor. Assuming smooth and limited movement
of the controls, the placard or "red-line" speed occurs where gusts
could meet the 4.67 limit load factor without any maneuvering.
(page 1-9)
Understanding
the Flight Envelope cont'd.: Normal placard speeds
are reduced 10% from design speeds to provide an extra margin of
safety. Thus, on the graph, the diagonal hatched area indicates
speeds at which you must use caution in maneuvers. You should neither
maneuver nor fly so fast as to expose your ship to loads within
the cross-hatched area marked, "NO". It can be inferred
from the graph that abrupt maneuvering in gusty conditions is dangerous
and can lead to very high "G" loads. In normal operation
the major cases of high "G" loads are tight spirals in thermals
which would not normally exceed 2 or 2.5 G's. Winch or auto towing
can produce high loads, but if the auto-winch placard speed is observed,
this will be within safe limits. The best ground launch climb is
obtained at speeds well below placard limits. Although the
2-33 is capable of performing some aerobatic maneuvers, they must
be done with extreme caution since it is very easy to greatly exceed
the placard or cautionary speeds in improperly executed maneuvers.
Inverted flight is not permitted. Aerobatics should not be done
without previous instruction in two-place aircraft.
(page 1-10)
2-33A GROSS WEIGHT and BALANCE CALCULATIONS
To Be Determined: 1.
Whether the actual CG of the particular 2-33 to be flown will fall
within the above limits. 2. Whether total gross weight
is not greater than the maximum allowable 1, 040 lbs. for any 2-33.
(page 1-11)
WEIGHT AND BALANCE CALCULATIONS SGS 2-33 or 2-33A
(page 1-12)
SCHWEIZER AIRCRAFT CORPORATION
ELMIRA, NEW YORK 14902 WEIGHT & BALANCE, MODEL
NO. SGS 2-33A SER. NO. __
369 __ REG. NO.
____N-33969___ DATE
February 27, 1975
(page 1-13)
(page 1-14)
(page 1-15)
SCHWEIZER AIRCRAFT CORP.
Form F-114 ELMIRA, NEW YORK 14902
3-78
ERECTION AND MAINTENANCE INSTRUCTIONS
MODEL SGS 2-33
SCHWEIZER AIRCRAFT CORP.
Form F-114 ELMIRA, NEW YORK 14902
3-78
SGS 2-33 - ERECTION PROCEDURE
A. TO REMOVE A/C FROM TRAILER 1. Remove trailer from towing vehicle and block wheels. 2.
Raise rear of trailer and block in position with sawhorse, jack
or other suitable means. 3. Remove wing-to-trailer tie-down
from wing tip skid brace from L. H. wing. (Note: R. H. wing is mounted
on the L. H. side of trailer and L. H. wing on R. H. side of trailer.)
4. Remove upper wing-to-trailer attach pin, support the
wing to prevent twisting. 5. Remove lower wing to trailer
attach pin and remove wing from trailer and place on ground.
6. Remove blocking means from rear of trailer. 7. Raise
and block the front end so that aft end of the trailer rests on
the ground. 8. Remove the rear tail wheel bracket-to-trailer
jack attachment, bolt and support fuselage. 9. Remove front
fuselage tie downs and carefully roll the ship aft out of wheel
well and off trailer into assembly position. B.
ASSEMBLY OF THE AIRCRAFT 1. With
the fuselage in an upright position, attach wing struts to fuselage
with (2) AN7 (7/16") bolts and #2 Commercial
safety pins. NOTE: The wing and strut
attach bolts must have a grip-length of 1-13/16" min., to avoid
threads in bearing. 2. Lift and place L. H. wing in position
and attach to fuselage with an AN7 (7/16") bolt in front fitting
and an AN6 (3/8") bolt in rear fitting. Install #2 Commercial safety
pins in bolts. (page 2-1)
(page 2-5)
(page 2-6)
(back cover) |