Re-timing, cleaning up (air
and fuel flow passages), freeing up (sliding friction), lightening and balancing
(removing unnecessary material),
and breaking in (initial running with rich fuel mixture while interfacing metal
parts fit themselves to each other) are all part of the effort necessary to create winning engines for
model racing events. This 1962 American Modeler magazine article predates
Schnuerle porting (in model engines), ABC (aluminum, brass, chromium) cylinder liners,
and modern metal alloys, but still the concepts are applicable to today's engines.
It purpose is to instruct on proper engine break-in so that it will have a long
lifespan.
Wankel lovers will appreciate the homemade engine shown.
Hot Engines!
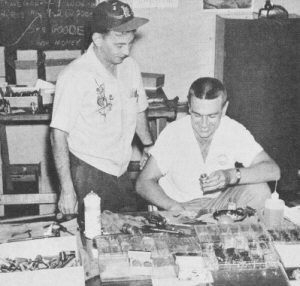
This has become one of the traditions of annual air-model National
championships: motor repair service operated by K&B. John Brodbeck (left) and
Bill Wisniewski try to figure how contestants can beat 'em up so.
Larrv Conover and Warren Kurth join forces to bring you this vital series; Part
2 next issue!
This report on speed and engine re-work is designed to give a comprehensive insight
into the methods and general approach used by experts in our various gas powered
events. This includes both control-line and free-flight power.
Perhaps the most important information we can pass on is the use of a scientific
method for improving the performance of your models. We will refer to the measurement
and recording of rpm readings throughout the text. The results you derive from "re-working"
depends on your ability to accurately measure changes in engine HP. The best
way is with the use of a good tachometer. So tachs are covered in this article.
Yes, you may be wondering why the engine manufacturer, with all his professional
know-how, can't put an engine on the market with ultimate performance built into
it. First of all, if it is to sell to the mass market it must operate easily and
efficiently over a variety of speeds and loads. By contrast., the hopped up speed
engine is tuned to operate at one specific high rpm while drinking large quantities
of expensive highly nitrated fuels. The modifications may also make it harder starting
and critical to operate. If it is run at a lower rpm its power will drop off rapidly.
Second reason is the limiting factor of economical production. The manufacturer
can not afford extensive hand work, or special materials (example: precision ball
bearings) if he is to keep the cost of his product within reach of the average modeler.
Engine rework can be classified under three main headings: RE-TIMING, CLEANING-UP,
and FREEING-UP. The last two terms are overworked catch-alls, but they do include
some basic methods and operations, so we explain them in general.
Re-Timing
The trend is to engines which turn faster on smaller props, and develop peak
HP at high rpm. Many engines can have their rotary valve timing modified to give
better performance in the 20,000 to 25,000 rpm range. Usually, opening the.
rotary valve port so that the intake closes later in the cycle will help. In fewer
instances, opening the valve port to let the intake open earlier may help, too.
But remember, the exact timing to be used is dependent upon several factors: Peculiarities
of the engine, its compression ratio, rpm at which it is expected to run, diameter
and length of venturi, bore-stroke ratio. All these factors are interdependent,
a change in one will nave an effect on the rest.
For example: Generally the rotary valve is still open for 40 to 60 degrees after
the piston has started its downward motion, building up crankcase pressure, and
tending to force the fresh charge of fuel vapor back out the venturi, However, the
momentum of the incoming fuel charge, due to its velocity build-up in the venturi,
will continue to carry fuel into the engine despite back pressure being developed
by the descending piston, As rpm increase, .this fuel charge velocity and momentum
builds up, therefore we can change the timing and leave the valve open a wee bit
longer.
Another thing we can do if we are going to run only at high rpm is to change
the cylinder port timing. Top edge of intake port may be filed ,upward to let the
port open earlier. Again, depending on the particular engine, the exhaust port may
be filed upward a greater or lesser amount than the intake port.
Height of piston baffle or dome will have some effect on timing. Filing down
the top of the baffle, or leveling it off on the intake side helps with some engines.
An interesting extreme is the Italian Super Tigre 15 which has no baffle on top
of a flat piston, while the intake and exhaust ports in the cylinder open almost
simultaneously.
"Cleaning-Up"
This is a term used to define all the modifications which make for easier passage
of the fuel mixture from the venturi opening to the combustion chamber. Most obvious
suggestion is to polish all surfaces over which the fuel mixture must flow, and
to radius and streamline all edges over which the mixture passes. Polishing thus
includes the connecting rod, crankshaft counterbalance, crankcase, bypass, and the
inside of the crankshaft - if the engine has a front rotary valve. The lower outside
edge of the cylinder intake port can be streamlined. Also the lower end of the bypass,
the edges of the connecting rod if it has a rectangular cross-section, and - if
a front rotary valve - the rear opening of the fuel passage. On some front rotary
engines, the venturi opening and crankshaft port opening may be lengthened and squared
out to match each other. Rear edge of shaft port can be radiused (details later)
and if shaft-port has been put in by milling flat across shaft, excess material
may be ground away. But be careful throughout all these operations that you don't
accidentally grind past the edge of the port and change the timing.
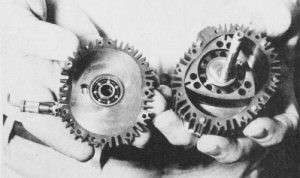
Remarkable engineering feat 2 years in development: revising
Wankel "pistonless" internal combustion engine for 2-cycle running. Floyd Nell,
St. Louis, did it: .50 c.i.d.; 10,000-rpm; all steel; ball & needle bearings;
20-oz.
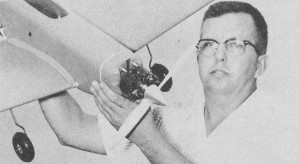
On some engines it helps to open out the throat of the venturi, but opening it
too much can give negative results. The optimum venturi size will vary with different
engine set-ups (rpm, timing, engine layout) so here again, investigate before you
operate.
If your engine has a front rotary valve and uses a rear crankcase cover, round
off the cover so that it does not obstruct the lower end of the cylinder bypass.
In general, the foregoing operations which comprise "cleaning-up" an engine will
produce the least gain per time expended in re-working and are of lesser importance
than the re-timing of "freeing" modifications.
One other point worth mentioning here is compression ratio - both cylinder compression
and base compression. The cylinder compression ratio may be varied for better performance,
but the governing factor will be the fuel you will be using and to some extent the
glow plug and cylinder timing. Most of the racing engines now have compression ratios
pretty well on the high side as they come from the factory. An old trick, especially
with the various McCoy engines, was to increase the base compression or "pack the
crankcase" by various means such as thinning down the connecting rod and shortening
the crankpin, which allowed facing off the crankcase to reduce Volume. The lightening
holes in the rotor disc were plugged with balsa also to reduce the crankcase Volume.
Such methods which worked well at lower speeds generally are not satisfactory at
today's high rpms.
"Freeing-Up"
This includes all the methods used to decrease mechanical friction in the
engine so that the greatest percentage possible of the energy released in the combustion
chamber can be transformed into useful horsepower at the propeller.
First step is cleanliness. This is extremely important. .Any re-working of parts
should be finished off with crocus and oil (or jeweler's rouge and oil) to remove
any trace of roughness. Then after any polishing or lapping, the parts involved
must be thoroughly scrubbed with a small stiff brush in hot soapy water. It is imperative
that every trace of foreign matter be dislodged from the pores of the metal or the
engine will soon grind itself to a worthless mess. Many a good engine has been ruined
at this point by a too-hurried cleaning.
Some engines as they come from the factory have the piston-cylinder fit set up
just a little too tight for high speed running. It is advantageous to lap these
out a little with jeweler's rouge or a fine grade of rubbing compound. It will take
some experience, or the advice of an expert on that particular engine to know how
much to lap. The engine must not be lapped out so much that it loses its compression.
Generally, as our operating rpm goes higher, we can stand a little more compression
loss for the sake of a free fit. Also, some engines benefit from a fine polishing
of all the wearing surfaces before they are even broken in.
The diametric clearance between the crankshaft and its bearing, on a plain bearing
engine, is important for free running at high rpm. Usually .001" for a 1/2A and
.002" for larger engines is the minimum acceptable - although in some cases, double
this amount of clearance will improve performance.
The bearing of a ball bearing engine should feel absolutely free of any tight
spots or roughness. So be careful to always keep bearings free from dirt, and so
not touch the ball races themselves. Perspiration from the fingers will ruin them.
A few drops of light oil after each day's running will help keep moisture from collecting
on the bearings.
Some modelers replace the ball bearings in their engines with high speed precision
bearings, but there is a catch here. The running clearance of a high speed bearing
is just as important, if not more so, than its precision for this clearance determines
the actual sliding friction and the loads imposed on the balls when the engine is
running. A precision bearing with the wrong internal clearance may do more harm
than good. Along this same line, the shaft fit in the bearing is very important.
So it's best to consult the bearing manufacturer for your particular application.
Port hooking is another robber of power. This is caused by the side loads which
result in slight tipping of the piston in the cylinder. What happens is that the
top lip of the piston catches on the top of the cylinder ports as it travels past.
A very slight radius or chamfer put on the piston lip and on the inside edges of
the cylinder ports will alleviate this. Some engines have this already done when
they come from the factory. Go very easy when doing any work inside the cylinder.
Any re-working which reduces the the strength of the part involved should be
held to a minimum. The more we reduce the strength of any part, the more it distorts
under load, causing binds and friction. And the net result may be a power loss instead
of a gain. This is a very important point to weigh when considering any reworking.
Turning down of cylinder fins is generally best avoided. Certain internal stresses
are set up in the metal of the cylinder when it is machined. When the outside fins
are turned down after the manufacturer has honed the cylinder to shape, some stresses
are released, which may disturb the balance and warp the cylinder.
When all the re-working has been done, the engine should be assembled carefully,
tightening all screws slowly and evenly, while checking for any binds in the engine.
If any binds are felt, the cause must be found and corrected before the engine is
run.
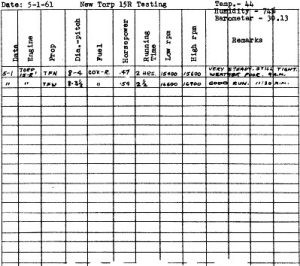
Here's how a dedicated researcher records his data on engine
performance; accurate measuring devices are absolute "must."
Breaking-In
This should be accomplished in a series of short one minute runs at high speed,
using a speed fuel that has plenty of oil in it. The reason for the short runs is
twofold - to prevent heating and to let the engine break in quicker on less running
time. The number of heating up and cooling off cycles is a factor in break-in. It
is best to break-in an engine at approximately the same speed that it will be run
in the air. The wear pattern on the moving and bearing surfaces changes with rpm
because the inertia forces of the reciprocating parts increase and the effective
pressure in the cylinder decreases with increasing rpm. By holding to one approximate
rpm throughout the life of the engine we have a better chance of keeping a nice
smooth wear pattern. Take for instance a plain crankshaft bearing which tends to
become oval as it wears. If we run it at various speeds it will, instead, assume
a rough clover leaf shape which produces extra friction and vibration.
Also at higher rpms there is less chance for shellac deposits to form on the
cylinder walls. This deposit, often referred to as engine varnish, usually occurs
with a new engine which is tight. A combination of tight fits, damp weather, and
fuel ingredients cause it to form. You spot it first when the rpm starts to sag
and the engine heats up abnormally. The engine loses it free feeling at the top
of the stroke (plug out). You can see it on the cylinder looking through the exhaust
port ... a sort of brownish film. It may be a little hard to recognize the first
time, but when you clean it off you will see the difference. There is no choice.
You have to remove it. Remove the cylinder and clean it with fine grade steel wool.
Molybdenum disulphide is an additive which should be used during break-in, either
in the form of a sub-micron powder which can be mixed directly in the break-in fuel,
or as an oil base suspension. Molyfilm, an oil suspension, has become the most popular
form of molybdenum disulfide with the speed fans. It is classified as a solid lubricant,
a slippery powder that has an affinity for soaking into the pores of the metal and
makes a thin film as little as one-millionth of an inch thick. This prevents metal-to-metal
contact and reduces the tendency for galling and seizure. The result is a reduction
in running time needed for parts to mate properly, and a reduction in engine wear
during break-in.
To check for a free fit, take out the glow plug and loosen the rear crankcase
cover of your engine. Oil it with a light oil and turn the shaft till the piston
is at the top of the cylinder. If your engine has been "freed" properly, the piston
will return to bottom dead center of its own weight. (Ringed piston engines excepted,
of course.)
Assuming that your engine has the basic layout and timing needed for speed work,
this business of "freeing-up" will have more to do with your engine output than
any other factor.
Lightening and Balancing
We might consider briefly this additional type of modification. So far very little
has been accomplished in this area, and then only via extensive experimenting. By
removing some weight from the reciprocating parts-piston, connecting rod, and wrist
pin - we reduce the inertia forces which the motor must overcome when it changes
direction twice every revolution. The net result is faster acceleration of the piston
during each stroke, and lighter loads on the bearings. However, there is usually
not a great deal for us to do here, since we encounter problems of distortion and
resultant binding when too much metal is removed. Also, the manufacturers have improved
this feature steadily over the years.
Balancing is another problem. Since the inertia forces caused by the reciprocating
parts vary with different rpms, it is impossible for an engine to be perfectly balanced
at all speeds. Therefore, it becomes a problem of balancing the system for the specific
rpm you wish to operate at. Unless you have a bad vibration problem it is best to
leave this balance set up as designed. If you do have excessive vibration you should
first check for unbalanced props, poor motor mounting, or a bent shaft.
So there you have the basic ingredients of a hop-up job. If you would like more
detailed recipes for your particular engine, go to contests and talk with some of
the experts. There have been some helpful hop-up ,articles in the past.
Dynamic Models Inc., 13755 Saticoy Street, Van Nuys, Calif., has published some
very good information on this subject in their "Tech Tips" ... their issue # 6 deals
specifically with reworking engines. Obtain same by writing to the company.
Posted February 5, 2023 (updated from original
post on 7/7/2012)
Articles About Engines and Motors for Model Airplanes, Boats, and Cars:
|